How can Virtual Reality be used in the Mining Industry?
Imagine this: It is early 90’s and a team of miners, clad in the dust, going deep into the earth with only basic tools and lanterns their way. This process is slow , dangerous and unpredictable. Fast forward to today, with the hard hats and heavy machines and drilling equipment, mining is on the verge of revolutionary transformation. But this time, tools are not only dynamites and drills, we have virtual headsets and 3D simulations.
According to the International Labour Organization (ILO) and other industry sources:
- Over 15,000 mining-related injuries are reported annually worldwide.
- An estimated 60-70 fatalities per million tons of coal mined occur globally every year, although the risks are even higher in developing countries.
- The average cost of mining-related accidents is over $4 million, including medical care, equipment damage, and loss of productivity.
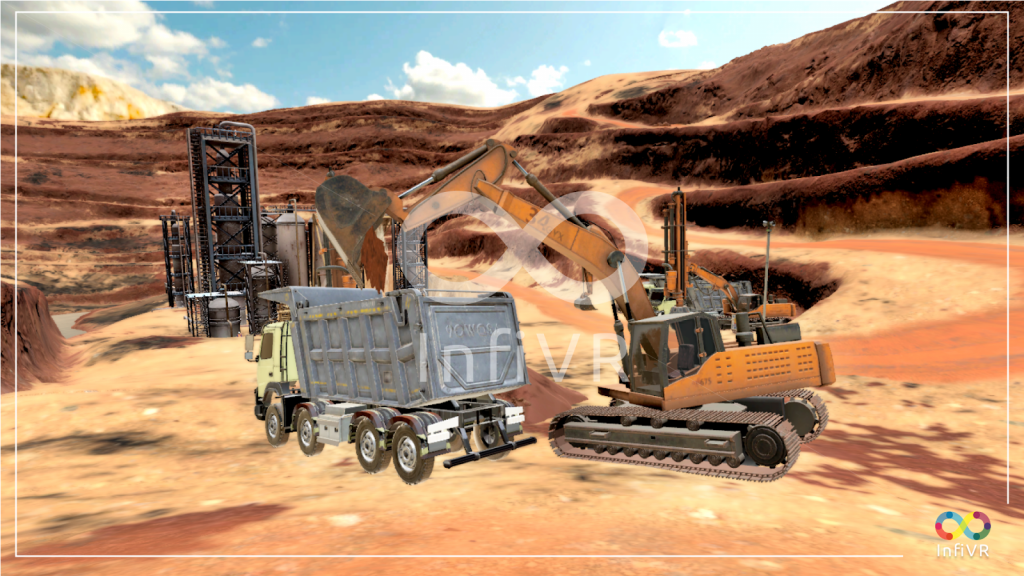
We all have heard of VR’s impact on safety training, however what if VR can transform mining far beyond just keeping workers safe? What if mining operations can be tested, optimized and designed without even setting foot in a mine? What if mining experts across the globe can collaborate in real-time, just walking through virtual representation of a mine as if they are present there.
This is future of mining – powered by Virtual Reality and InfiVR’s Immersive Solutions.
Redefining Exploration: A new path for Geologists
Traditionally, geological exploration has been a manual process. Geologists trekked into deep and remote areas, collected physical samples and returned to their labs to combine together geological models. While satellite systems and other surveying tools improve on this approach, virtual reality takes it to another level. Geologists can now, through virtual reality, explore mining sites from their offices by using immersive 3D models of terrain. Such models are produced using drones, satellites and sensors offering detailed views of the landscape. They can observe rock formations, mineral deposits, and even uncover how excavation impacts the environment. It enables early and accurate decision making during the exploration process.
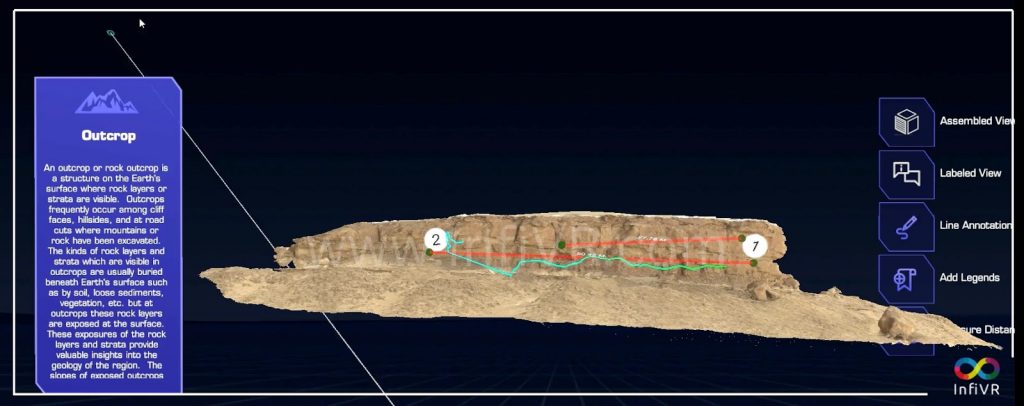
InfiVR offers state-of-the-art VR tools designed for geological analysis and interpretation. What was traditionally done on 2D computer screens can now be accomplished in an immersive 3D environment using InfiVR’s immersive geological analytical and interpretation software. This tool allows geologists to visualize and interact with data in a more intuitive and efficient manner, leading to faster insights and more accurate predictions.
By integrating VR technology into geological exploration, InfiVR empowers professionals to enhance efficiency, minimize risks, and make better-informed decisions that drive success in mining operations.
Designing the Perfect Mine: Virtual Optimization
Once a mining site is found, the next step is to design a mine that ensures efficiency and reduces risks. Conventionally, engineers used only 2D sketches and physical models, which made it difficult to understand the mine’s layout complexity. With VR, engineers can design and optimize mining operations in a fully immersive 3D environment. The engineers can test excavation techniques, optimize machinery placement and run simulations to predict wear and tear without moving a single ounce of sand. For example, the world’s largest mining company, Barrick Gold, started using VR to model their operations, which is helping them fine-tune not only the extraction processes but also visualize risks and bottlenecks before breaking ground.
Digital twins: Real-time decision making
Digital twins, an exact virtual replica of mines, is the most advanced development in VR for mining.These are dynamic models which update themselves in real time in case any conditions in the mine change. This helps operators to monitor and control mining operations remotely through a visual interface. Also, any mining company have fleet of trucks working day and night. And if the truck breaks down it would mean expensive delay but using a digital twin it can be tracked virtually which could give them a clear performance of trucks with its wear and tear. So it has an unplanned downtime reduced to its lowest, hence better life of the heavy machinery.
InfiVR is working with leading mining companies and research institutions worldwide, using advanced Immersive VR technology to transform decision-making and optimize operational efficiency. InfiVR’s Immersive solutions enable critical mine planning decisions and deliver unparalleled efficiencies in mining operations through digital twin simulations.
Mines utilizing VR for safety drills have reduced evacuation times by 35%
Work Environment
Underground work environment can be described as dirty, dark, wet, noisy, hot and dangerous. Workers in the mining industry can develop several hazards like working in confined spaces, working in steeply inclined excavations, handling heavy material and equipment, working in proximity of moving machinery. VR can train the miners. Through immersive solutions, workers can be given exact replicas of underground environments with no risks at all. Such virtual exposure enables them to prepare for the real-life situation in a controlled setting. This eventually makes their reaction time improve and helps in reducing accidents on-site.
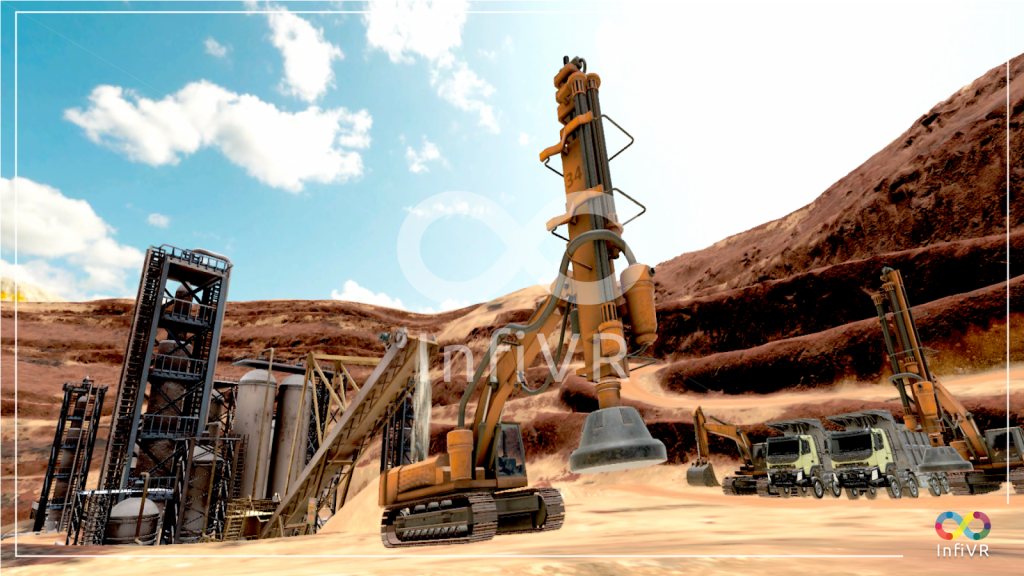
Using VR for safety training at Goldcorp’s Éléonore mine in Quebec reduced safety incidents by 30%, showing how effective it is for preventing risks and building skills.
Some Case Studies of VR in Mining
1. Caterpillar’s Virtual Mining Initiatives
Caterpillar built a virtual mine at its Mossville, Illinois, facility. It operates 24/7 with 350 simulated machines over 25 square miles. The virtual setup helps test and improve equipment and processes before using them in real mines, boosting efficiency and safety.
2. JCB’s Virtual Reality Training Programs
JCB is using VR training programs to enhance operator skills and safety. The simulation of realistic virtual environments allows operators to practice using machinery and safety rules without the risk of on-site training. The method has increased operator skills and decreased workplace accidents.
3. BHP
BHP utilizes VR to provide virtual equipment training for heavy machinery operators, such as drills, haul trucks, and excavators. The company has reduced the amount of equipment damage caused by operator error and accelerated the onboarding process for new employees by 40% by practicing in realistic, risk-free virtual environments.
4. Vale
Vale leverages VR modules for emergency evacuation and procedural training. Workers can practice evacuation procedures for scenarios like mine collapses and underground fires in a realistic and safe setting. As a result, this approach has reduced evacuation times by 35% and significantly decreased on-site safety incidents.
With the integration of Virtual Reality (VR) and Augmented Reality (AR) technologies into mining, incidents are promising to be reduced. Workers involved in VR training undergo dangerous situations that might happen in the workplace, hence having an appropriate response. Research indicates that such immersive learning can result in a 45% increase in knowledge retention with a significant reduction in the number of accidents.
InfiVR is leading this change towards a future in mining. Furthermore, our innovative solutions allow workers to get real simulations of potentially dangerous scenarios, prepare for emergency response skills, and hone their skills further. Moreover, teams can work effectively inside the shared virtual space using InfiVR’s innovative technology, thus improving communication and decision making. The future of mining is brighter and safer with InfiVR’s groundbreaking solutions.
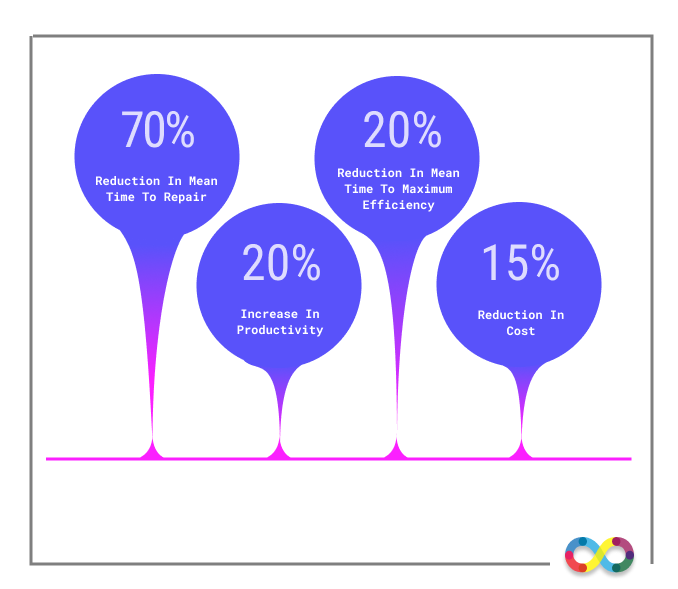
Embrace our solutions and change your mining business today—safety and efficiency should not be compromised at any cost.
Contact us at hello@infivr.com