How AI and Digital Twin technologies can be used in the Oil & Gas Industry?
Oil and gas is the industry where every second of downtime can cost thousands and these operations rely heavily on experience, gut feel and fixed schedules. Maintenance teams service equipment based on a calendar rather than the need and any downtime from unexpected equipment failures is an unavoidable cost of doing business. Rig operators, working in extreme and remote environments, have limited data to guide them—often making critical decisions based on experience and intuition alone.
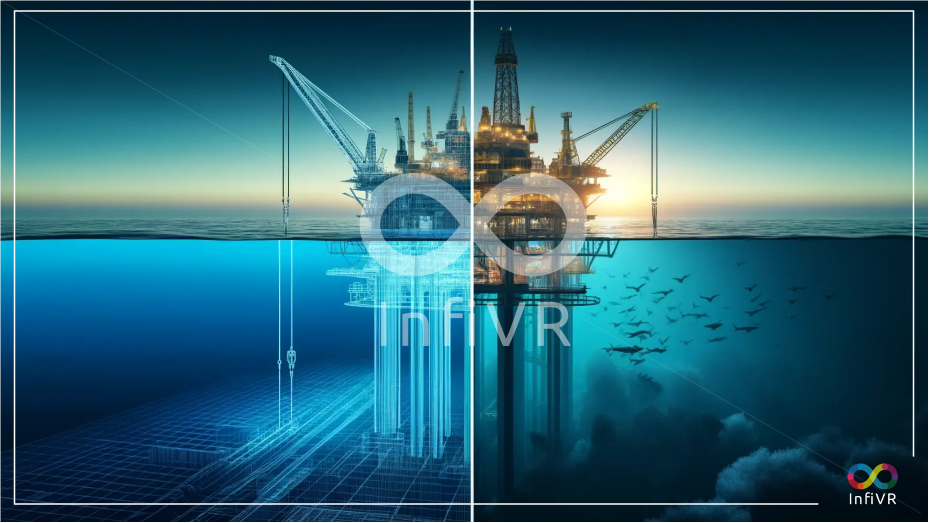
According to McKinsey, over two-thirds of the world’s oil production facilities are equipped with advanced connectivity, yet many aren’t leveraging its full potential.
Today, AI-Powered Digital Twin technology has completely transformed this traditional approach . Whether it’s a deep-sea oil rig or an expansive refinery, virtual replicas of these assets offer real-time insights, enhancing operational efficiency and predictability.
Let’s explore how digital twins are elevating the oil and gas sector by examining real-world applications that extend beyond the typical discussions of safety and training.
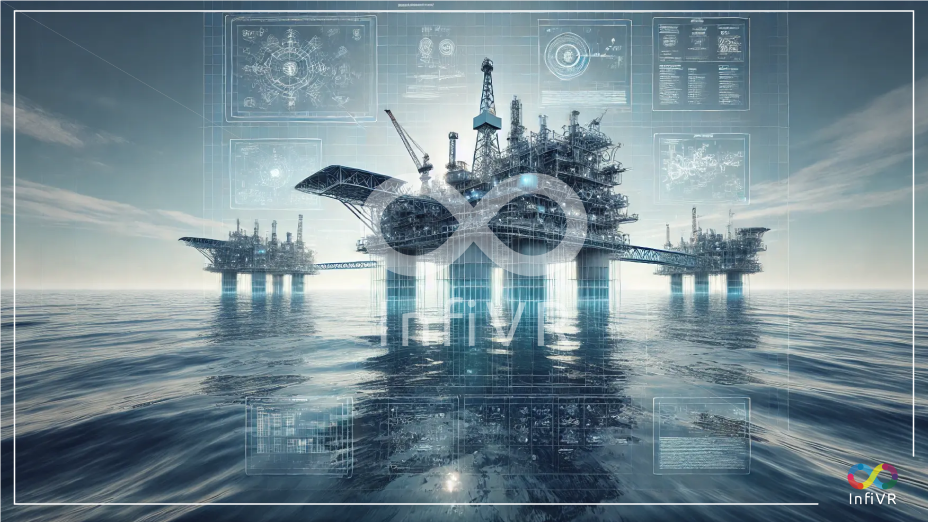
Unscheduled Downtime & Forecasted Maintenance
Unplanned Downtime in oil and gas industry is tackled by digital twins by enabling predictive maintenance. Digital twin flags any potential issues before they lead to a breakdown.
Consider BP’s offshore rigs, digital twins continuously monitor compressors and turbines. Instead of waiting for equipment to breakdown, BP engineers receive alerts & can intervene early minimizing the unplanned downtime. This reduces repair costs and keeps operations running smoothly
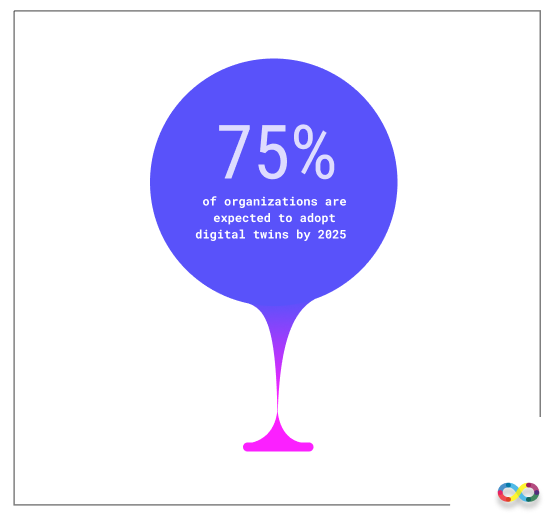
75% of organizations are expected to adopt digital twins by 2025
Real-time monitoring of Remote and Offshore assets
Assets which are located in remote or under water locations, for them monitoring is difficult and costly. Digital twins address this by allowing real-time and remote monitoring. Operators operate vital parameters like temperature and pressure, flow rate without physically present.
Equinor uses digital twin to keep close watch on their underwater equipment. By using these virtual monitoring systems, engineers make quick adjustments before it disrupt production. This also reduces costly offshore site visits and troubleshoot the systems remotely.
Supply Chain Optimization and Logistics
The movement of crude oil from one place to another use pipelines, ships, trucks and storage facilities. A delay at any point can cause bottlenecks and missed deadlines.
Digital twins offer oil and gas industries a real time view of their logistics feat enabling them to quickly respond to any disruptions and optimize inventory levels.
Many companies use digital twins for their supply chain network to predict and adjust to demand fluctuations, extreme weather. Result? More efficient supply chain with less interruptions and more profit.
Digital twins and intelligent data systems could enable oil and gas operators to reduce total decommissioning project costs by up to 15%.
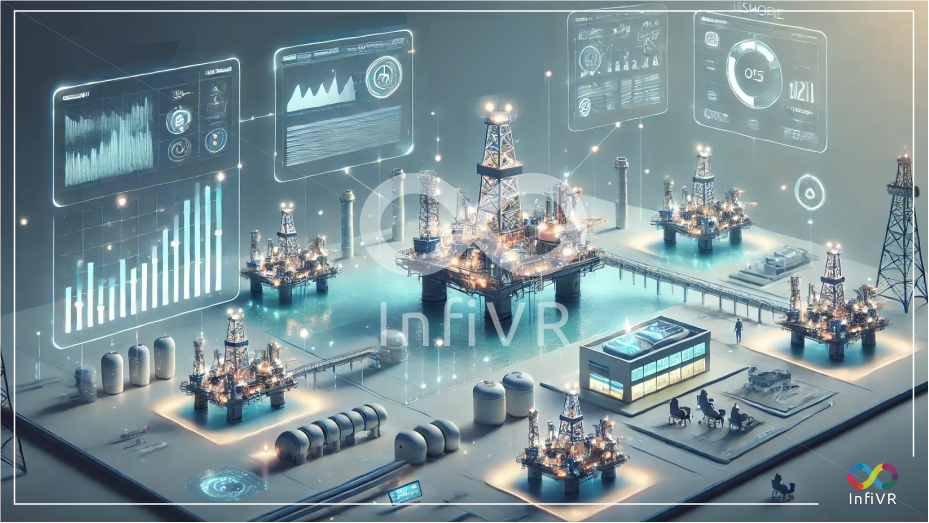
Virtual Training to navigate & operate
Safe and sustainable operations of oil and gas facilities depend on level of training and experience of employees. Challenge of ‘big-crew change’ is faced by this industry where experienced workers retire in near future and transferring training to next generation is affected due to cultural and demographic challenges. Digital twin together with AR, VR, Spatial Computing, and the Metaverse offer virtual platform to train new employees in navigating within facilities, monitor and inspect systems and giving full exposure of oil and gas facilities. Such virtual training can help reducing number of interruptions or accidents that may occur while training new employees.
Major oil and energy companies like Shell, ExxonMobil, Chevron, Saudi Aramco, ADNOC, BP, and TotalEnergies use AI-powered digital twins. Let’s see how it helped them:
1. Shell
Shell uses AI-powered digital twins to improve efficiency and sustainability in its energy facilities. These digital twins use real-time data from IoT sensors to optimize energy production, check equipment health, and lower emissions. For example, at Shell’s Prelude floating liquefied natural gas (FLNG) facility, the digital twin system predicted and prevented potential downtimes, saving millions in unplanned maintenance costs annually. Shell reported a 20% improvement in operational efficiency at its facilities leveraging this technology.
2. ExxonMobil
ExxonMobil has adopted digital twin systems in its downstream and upstream operations to simulate refinery processes and optimize plant performance. These models use AI to analyze vast datasets, improving energy consumption and reducing CO2 emissions. For example, using digital twins in its refineries, ExxonMobil has achieved 10% decrease in energy consumption and a considerable reduction in maintenance costs.
InfiVR has collaborated with ExxonMobil to provide state-of-the-art AI-based solutions, leading to innovation and efficiency in their operations.
3. Chevron
Chevron utilizes digital twins to streamline reservoir management and optimize production. By integrating seismic data, geological models, and real-time drilling feedback, Chevron improved decision-making and reduced exploration time. This approach has increased production rates in specific assets by 8–10%, enhancing profitability while ensuring safety through predictive maintenance systems.
4. Saudi Aramco
Digital twins powered with AI are used by Saudi Aramco to visualize and optimize its oilfields, refineries, and petrochemical plants. These toolsets ensure up to 15% cost savings in operational expenditure and increase planning accuracy for productions. Its digital twin platforms help in achieving sustainability goals such as reducing methane emission up to near zero by 2030.
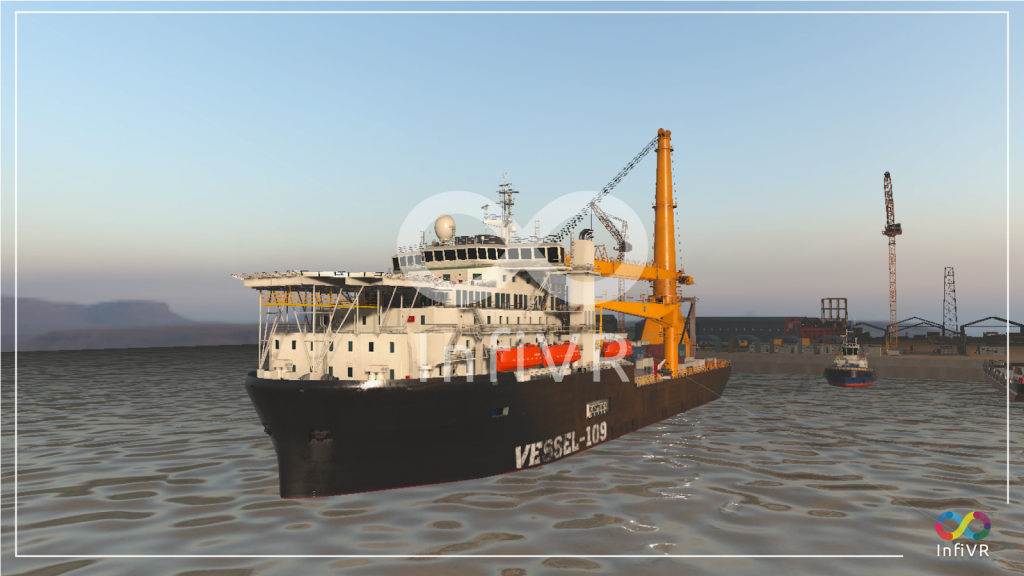
InfiVR has partnered with Saudi Aramco to deliver high-end AI-based training solutions customized to their operational requirements. These cutting-edge solutions not only enhance workforce skills but also serve additional purposes, such as improving safety, optimizing performance, and ensuring operational excellence in the energy sector.
Are you prepared to embark on the next chapter of your oil and gas business?
InfiVR, your partner in AI powered Digital Twin Technology can help you transforming your oil and gas facility and you can leverage digital twins to predict equipment failures, optimize drilling paths prior to setup, and monitor emissions remotely. By integrating Spatial Computing, InfiVR’s metaverse based innovative solutions help organizations to enhance their operational efficiency and make informed decisions for their sustainable growth
Watch InfiVR’s AI-powered immersive technology in action!
How InfiVR VR Training Improves Oil Rig Safety
This video showcases how InfiVR VR-based immersive training prepares blue-collared workers to handle emergencies on oil rigs, enhancing safety protocols and reducing on-site risks.
Immersive Mechanical Training for the Oil & Gas Industry
Explore how virtual simulation reproduces such difficult mechanical exercises for training workers with skill without operational delay.
Use this cutting-edge technology and position your business at the forefront of the industry — The future awaits!